THE PROCESS OF DEVELOPING A NEW PRODUCT
- elitehandbag
- Nov 7, 2020
- 3 min read
Updated: Nov 12, 2020
We often get asked what the process is when creating a product from scratch. So, we thought it would be useful to offer a guideline to illustrate how the process usually works with us.
The quickest way for us to understand your idea is to see a drawing. It doesn’t have to be well-drawn, nor does it have to be a CAD or tech pack. If you can note down some rough measurements, we can figure the rest and nail the final proportions at the pattern-making stage.
Emails are great, but a phone call/visit is often the quickest and most effective start. For international clients, we have access to Skype and WhatsApp, which can help to save on any costly calls. With the right Q&A’s, we get an insight into what is in your head and start to build ourselves into your ‘team.’ So it helps to know if the bespoke item is a private commission or a sample which may go into production. Is there a deadline or a budget? What materials are you hoping to use?
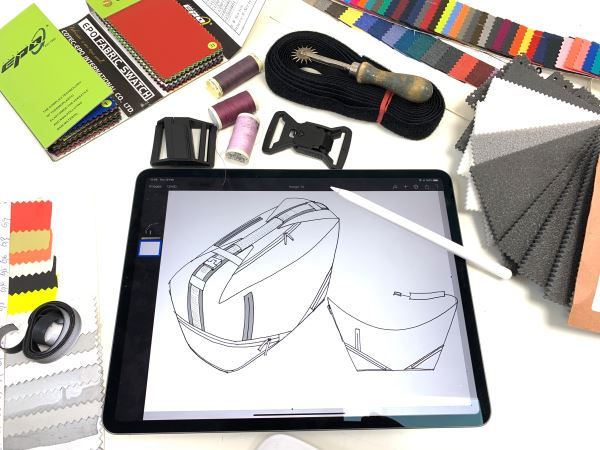
Any mock-ups, material samples, inspirational photos help enormously. The bigger the goodie bag, the better and don’t think all this stuff needs to look like it’s come out of a design studio. Staple up some cardboard from a cereal packet, get an idea of shape and scale.
A heads up now. Projects like this take time. Probably a lot longer than people expect. Remember, if it were easy, then everyone would be doing it. Design houses have money, professional teams to design, source materials and liaise with factories. If you are a start-up, then it’s just you, or maybe you + one and your regular job and busy life will get in the way in between everything else we are working on with you. You may have already invested time and money with another maker, and you are feeling like it’s going on forever. This feeling of exasperation is normal. So just breath. From a seed of an idea to a finished sample can potentially take twelve months by the time you’ve gone around the block a few times. It may be less, but it’s more likely it will be longer.
While we’re waiting for components, we can create a toile/mock-up to help visualize your product. A tangible 3D version is quite different from a drawing (remember the cereal packet?) so, at this stage, you may find you wish to make amendments.
Once you’ve seen the mock-up and approved any swatches, we can get started! We’ll keep in contact each step of the way, and if there’s a decision to be made, we’ll request your approval before going ahead.
Creating a WhatsApp group, including everyone involved in the project is a great way to share ideas, questions and images of work in progress. It’s quick and handy to use when you can’t take a call or get to your laptop.
We bill by the minute so, you’ll find stopwatches dotted all around the studio. We flick them on when working on your project, and off when we’re not. We then note this time on your job sheet.
We work with a diverse range of designers, and each has their way of working. We will fit with you best we can, and we have a ‘can-do’ attitude. Happy to move an idea forward with you, help when you are stuck and pick up the phone whenever you call. You will know each of us by name, and you will be dealing directly with the person who is cutting your pattern and making your sample. We are honest and trustworthy and have a solid reputation in our industry, so confidentiality is a given.
Comments